Basic of Aluminium Gravity Die Casting
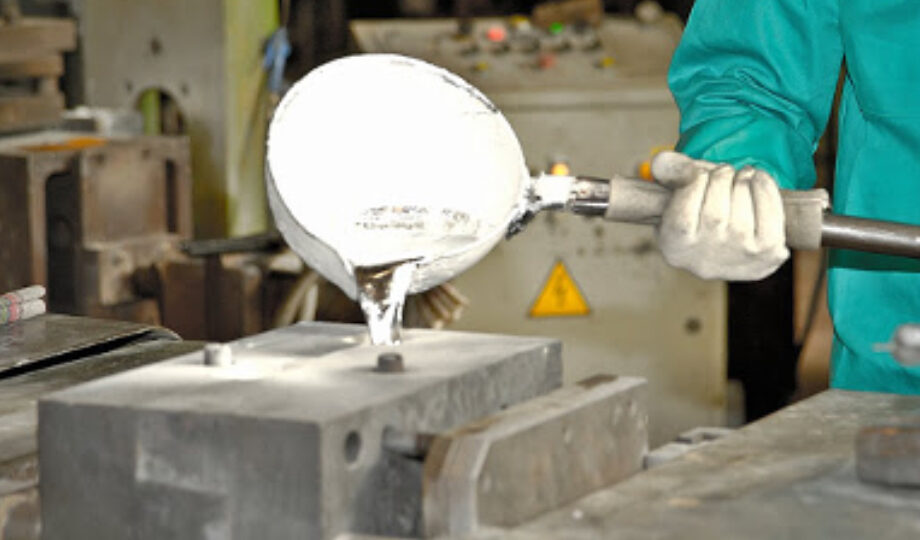
Aluminum gravity die casting is a widely used manufacturing process that involves pouring molten aluminum into a reusable metal mold (die) under the force of gravity. This method is known for producing high-quality, dimensionally accurate castings with good mechanical properties. Below is an overview of the process, its benefits, applications, and more details.
Process Overview
Mold Preparation:
The process begins with the preparation of the die, which is typically made from steel or cast iron. The die is designed to have a cavity in the shape of the desired component.
The die is preheated to the required temperature to avoid thermal shock and is then coated with a refractory material or a mold release agent to facilitate the easy removal of the casting.
Melting and Pouring:
Aluminum is melted in a furnace to the appropriate temperature (usually between 660°C and 750°C).
The molten aluminum is then poured into the die. Gravity alone is used to fill the mold cavity, without the need for additional pressure or vacuum.
Solidification:
Ejection and Finishing:
Once the casting has solidified, the die is opened, and the casting is ejected, typically using ejector pins.
The casting may then undergo various finishing processes, such as trimming, machining, sandblasting, or coating, to achieve the desired surface finish and dimensional accuracy.
Benefits of Aluminum Gravity Die Casting
High Dimensional Accuracy:
Superior Surface Finish:
Good Mechanical Properties:
Components produced through gravity die casting typically exhibit good mechanical properties, including strength, hardness, and fatigue resistance, due to the finer grain structure achieved by controlled solidification.
Reusability of Molds:
Versatility:
Material Efficiency:
Applications of Aluminum Gravity Die Casting
Automotive Industry:
Gravity die casting is extensively used in the automotive sector to produce components such as engine blocks, cylinder heads, transmission housings, and various structural parts.
Aerospace:
The aerospace industry uses this process to manufacture parts that require high strength-to-weight ratios, such as brackets, housings, and other structural components.
Electrical and Electronics:
Industrial Machinery:
Consumer Goods:
This process is also employed in the manufacturing of various consumer products, such as cookware, hand tools, and decorative items, where aesthetics and durability are important.
Advantages over Other Casting Methods
Compared to Sand Casting:
Compared to High-Pressure Die Casting:
While high-pressure die casting is faster and more suited for high-volume production, gravity die casting is less expensive for lower volumes and produces parts with fewer porosity issues, leading to better mechanical properties.
Compared to Investment Casting:
Limitations
Initial Tooling Cost:
Design Constraints:
Cooling and Shrinkage Control:
Conclusion
Aluminum gravity die casting is a versatile and efficient process that offers high-quality results for a wide range of applications, particularly in industries where strength, precision, and surface finish are critical. While it has some limitations, particularly in terms of initial tooling costs and design complexity, its benefits in terms of material efficiency, mechanical properties, and overall cost-effectiveness make it a popular choice in many manufacturing sectors.
Dongrun Casting has 20000 square meters of facility houses and 200 production & test equipment, From quotation and tooling design to casting and finished machining, we can work with you at every stage. We serve a wide range of industries-from Fortune 500 corporations to small and midsize OEMs. Our products include Automotive&trucking, Electric Utility & Communications, Metering Systems, the Hydraulic Industry, Medical Devices, Lighting, Fuel and Gas Pressure, and Furniture parts.
More Details: www.dongruncasting.com